World Forestry Center’s Discovery Museum was featured in Issue 2, 2020 of Wood in Architecture magazine. View it online here or read the full article below.
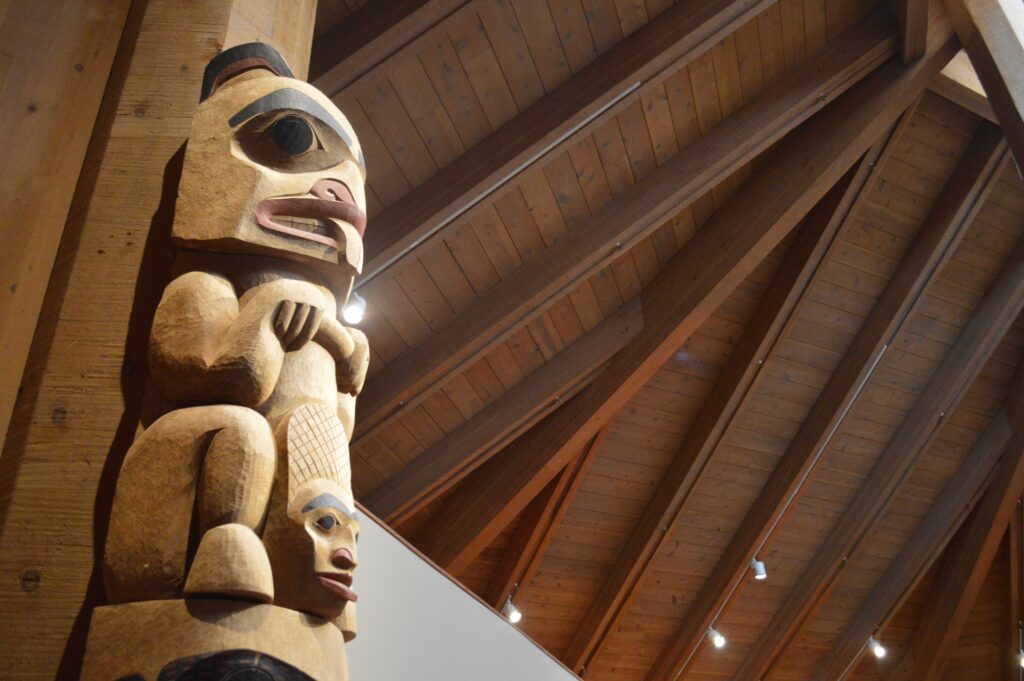
World Forestry Center’s Discovery Museum Highlights U.S. Species
Located in Portland, Oregon, USA, the roots of World Forestry Center date back to the 1905 Lewis and Clark Exposition in which a massive log structure was built to house the Forestry Building. Rebuilt in 1971 in Portland’s wooded Washington Park, the non-profit’s 20,000-sq-ft Discovery Museum educates visitors about forests and forestry in the Pacific Northwest and around the world.
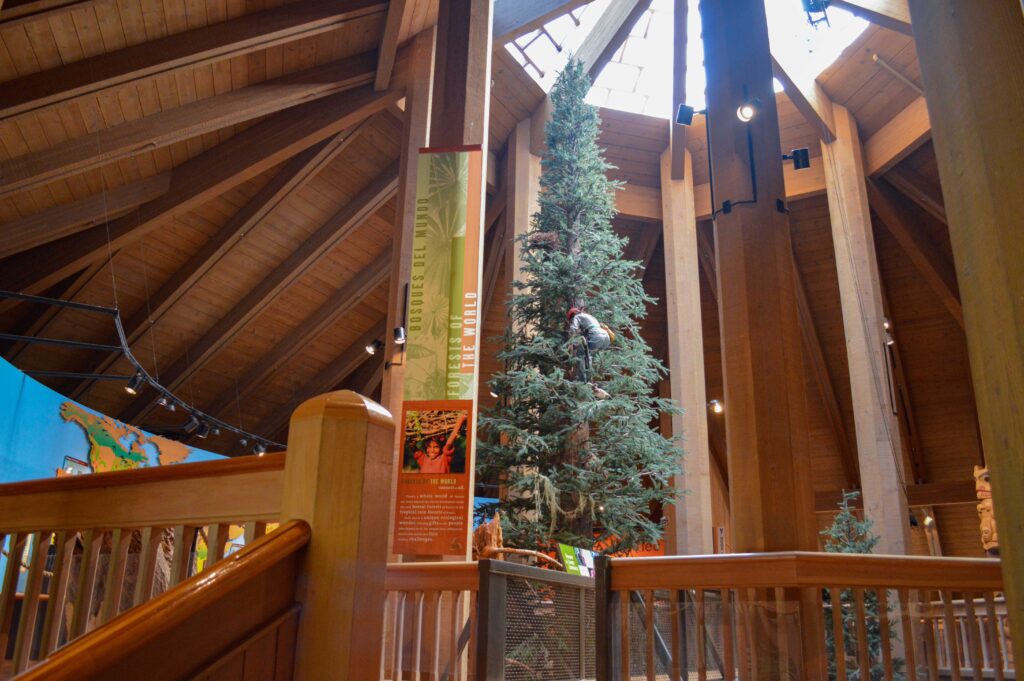
Designed by internationally known Oregon architect John Storrs, the Discovery Museum opened in 1971. The museum was designed to be an example of wood construction and a tribute to craftsmanship with wood. Special care was used in selecting a variety of fine woods for use throughout the building, and a talented team of artisans, carvers, and craftsmen was assembled to build the museum.
Upon approaching the museum expansive sloping roofs dominate exterior. The sharply pitched overhangs of the roof are supported by carved posts of coast redwood (Sequoia sempervirens) from the northern California coast. These posts were hand carved by five local artists and depict different aspects of forestry life. The outer walls of the museum are rough-sawn, 1inch x12 inch western redcedar (Thuja plicata) boards applied vertically. The rafters extending from the main wall are Idaho white fir (Abies concolor). The massive horizontal headers above the redwood posts are Douglas-fir (Pseudotsuga menziesii).
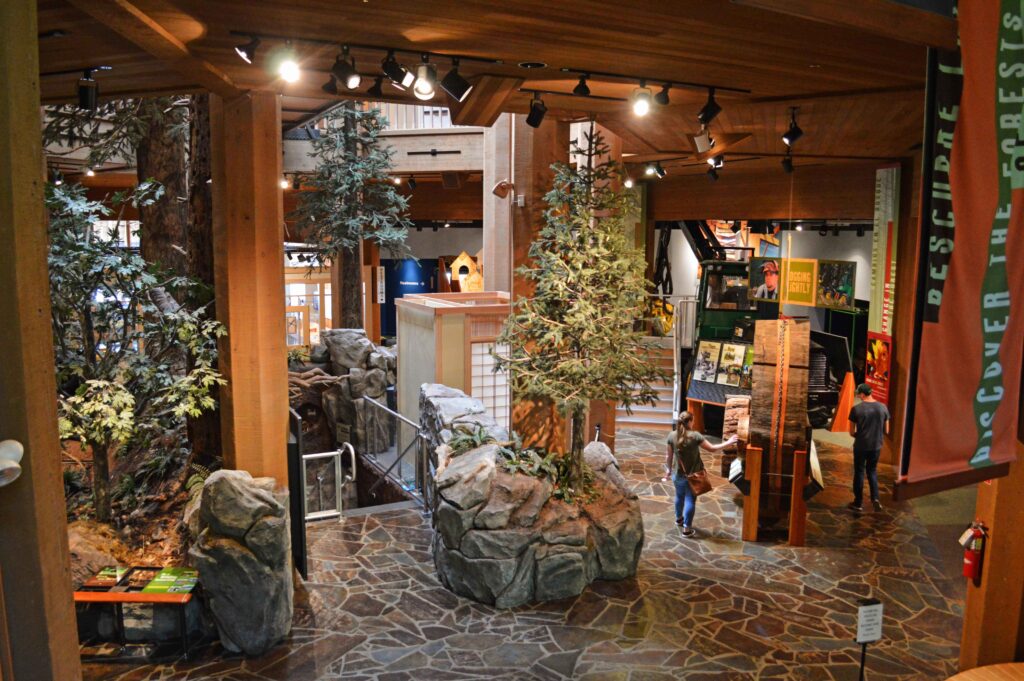
The exterior design of the museum complements the interior. In the entry foyer, laminated Douglas-fir beams in the ceiling support the Mt. Hood Room that was added during a 2005 renovation. Visitors have their first look into the central rotunda and the attractive forest exhibits in the building. Five different types of wood are used on the beautiful, curved wall to recognize major donors to World Forestry Center since 1964.
The spacious rotunda at the center of the building is dominated by eight pillars stretching 60 feet (18m) to the skylight dome. The pillars are joined to form an octagon around the central exhibit featuring the Dynamic Forest. The core of the pillars is Douglas fir lumber, laminated in a heavy cross pattern. Their eight-sided shape is achieved by mitering the edges of fir boards and fitting them across the notches. Laminated Douglas-fir beams frame the skylight dome high above.
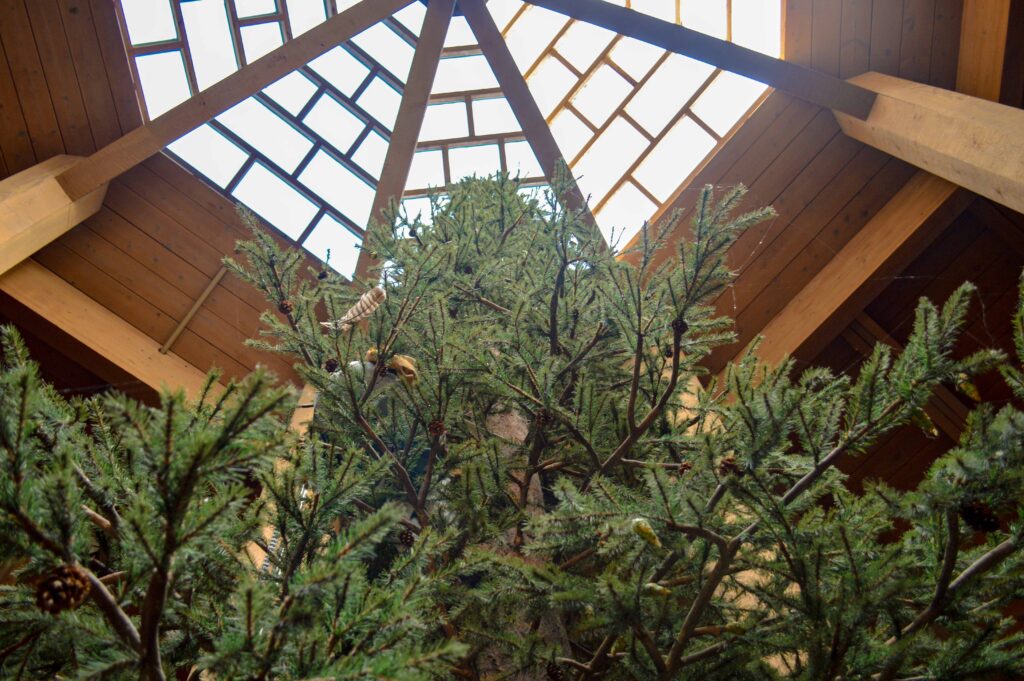
Large horizontal beams of Douglas fir, measuring 9 by 36 inches (23x91cm) support the rest of the second floor. The ceiling of the first floor is western red cedar paneling.
The second floor is made from thousands of 2×6 inch pieces of Douglas-fir, placed end-grain up to reveal the heartwood, sapwood, and annual growth rings of the original trees with their rich variations of light and dark. The blocks are only 1.5 inches thick, but are pressure treated for durability. Developed for warehouses, the end grain, once saturated with varnish, is more resistant to rolling wheels than is concrete.
The vast ceiling of the second floor is supported by Douglas-fir beams that are doubled in place with a space between members for sprinkler piping and wiring. Laid at right angles to the beams is 3 by 12-inch (8×30 cm) ponderosa pine (Pinus ponderosa) decking.
Finally, a special exhibit to educate users about new technologies in wood building materials includes information about the manufacture and use of cross laminated timber. Cross laminated timber is gaining popularity around the world as a beautiful and durable material in multi-story wood frame construction.
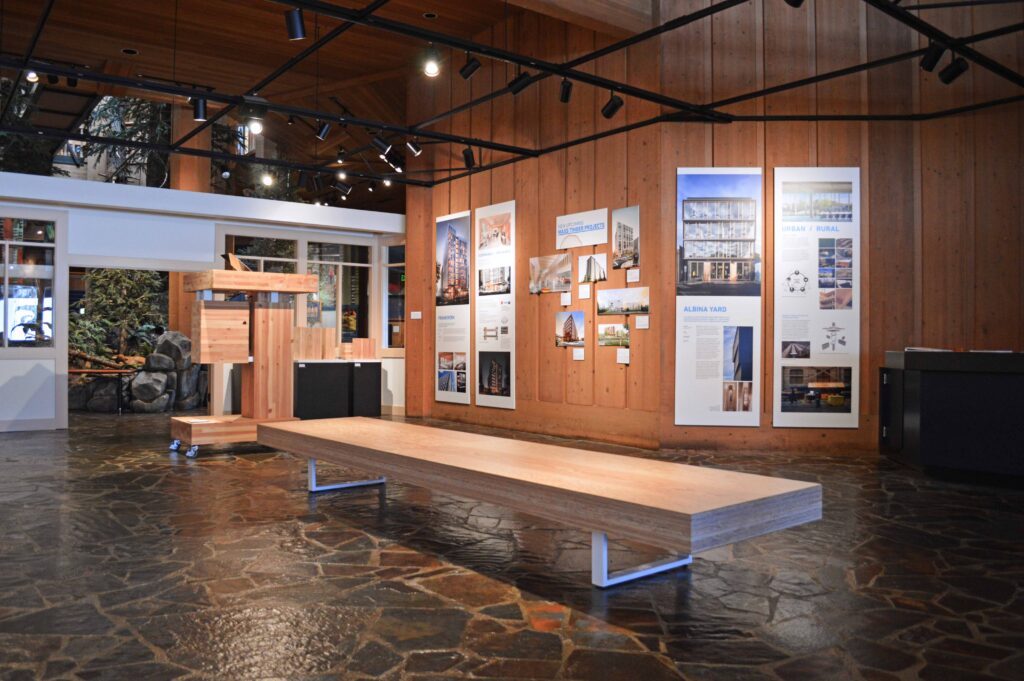
The walls of the exhibit room are paneled in sugar pine (Pinus lambertiana) from the mountains of southern Oregon. The species was regarded by early American lumbermen as the “King of the Pines.” The common name derives from the edible sweet resinous sap that exudes from cut or partially burned heartwood. Boards measuring 1” by 12” are vertically installed. These are accented by tapered battens that cover the vertical cracks, and a smaller tapered molding applied at right angles to cover each end joint.
Photo and article credit: World Forestry Center